Oilfield, your supply chain is inefficient and broken because it is outdated. You still fax paperwork or receive faxed documents. You still hand-write some of your orders and receive handwritten trucking sheets. You still call a dispatcher to check in on the delivery. You still wait for the original of a BOL to arrive back to you. Just like those who came before you did in 1985.
How many other things in your life are just like they were in 1985? (If you were even alive then). Not many. Imagine how difficult things would be if you still only had a home phone, antenna TV, or a camera with film and disposable flash cubes. Or if you still had to two-day air or OVERNIGHT important documents so they’d get there quickly instead of emailing them.
But we digress, you get the point.
Your supply chain is, “like totally,” inefficient because it is working within an incredibly old framework – which is being sternly protected by “that’s the way we’ve always done it, and we don’t have the time or resources to change it.”
Sure, you’ve updated some things. You use email. You send texts. But the big stuff – you are still doing it the most inefficient way possible.
You invest a lot of resources in qualifying your supply chain. But you invest almost ZERO resources in making it visible.
Here’s a quick story highlighting these inefficiencies – don’t be surprised when it sounds familiar to you.
ABC Upstream had a new drilling program. Eight wells, 6-month rig contract.
ABC had a detailed plan from rig up to tear down, including the best rig hands in Texas.
ABC procurement vetted the suppliers and had the best prices with the highest quality equipment and service levels from drill bits to casing.
Yet, when it came time to receive supplies and schedule crews; something happened. Things fell off schedule – and efficiencies were lost.
ABC called in the pending casing on Monday morning and requested it to arrive by Tuesday at 4pm. The crews and forklift would be waiting, and at ABC’s drilling pace, they’d be ready. ABC checked in with the supplier Tuesday morning. The supplier checked in with trucking, all was confirmed.
Tuesday at 3:50pm, no casing. ABC called the supplier. Supplier called trucking. ABC nervously waited. Should they call someone local? Should they pay the crews to standby? How much longer? When should they interrupt the big boss? ABC got a call back around 4:15. Trucks 1 and 2 were held up loading and should arrive by 5:45. Truck 3 was MIA. Dispatch was searching.
ABC decided to pay the crews’ stand-by time; they’d try to get reimbursed by the trucking company or supplier later. ABC waited – the crews were getting antsy; another rig wanted them for a casing delivery nearby. 5:45 turned in to 5:55. ABC called the supplier, they called trucking, ABC waited.
Two trucks showed around 6. Two hours behind. Not too bad. A few thousand dollars lost. But the third truck? It finally arrived around 6:45. It was missing critical crossovers! Big expense. Big delay. Whose fault? The supplier claimed they ordered the right thing. Fingers started pointing. The yard said they provided a BOL showing no crossover on the truck. The driver said it matched documents he had. Who will pay the hotshot, loss of back haul, extra rig time, and other fees?
Will ABC be able to get all 8 wells drilled in 6 months now? At $25k a day for the rig, how much will this delay cost?
Maybe you don’t yet notice how blatantly inefficient this is. In 1985 you wouldn’t have noticed how annoying it was to only have a home phone – that didn’t even have caller ID. You didn’t know anything else could even exist.
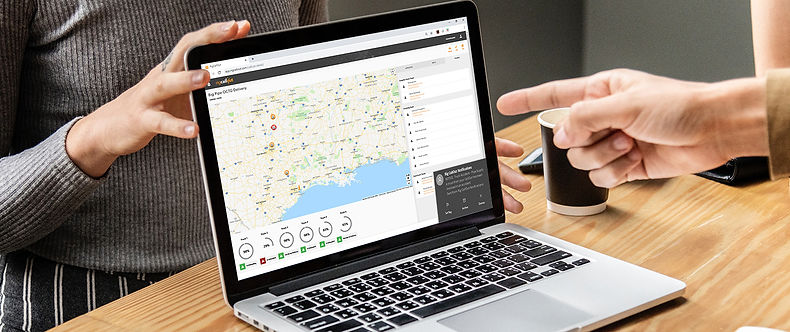
These Supply Chain Visibility issues are detrimental to any project and budget.
Fortunately, there is a way to fix them. Proactive communication. Robust and affordable technology to unite the entire supply chain.
Here’s the same exact scenario if ABC had used the new Internet of Supply Chain technology – Rig CallOut.
ABC put the casing order in Rig CallOut (Actually, their supplier did it for them.) Within minutes ABC received confirmation from the supplier, trucking company and drivers that the products would ship when requested.
ABC received an ETA for each truck. Then check-in notices directly from the drivers. They even received BOLs and photos of the loads uploaded by each driver at the yard, so they knew the right equipment was loaded.
ABC received communications directly from the drivers. ABC had a dashboard showing where each truck was on a map and whether the truck was moving or stopped.
When trucks got delayed at the yard, ABC knew at 1:30 instead of 3:50pm. The ETA was modified. They were able to reschedule the required teams.
When truck 3 was loaded at 1:45, ABC and the supplier got a photograph and saw it was missing the crossover and noticed it missing on the digital BOL. ABC told the driver. He turned around and reloaded the missing crossover. The delivery stayed within an hour of the original schedule.
Proactive versus reactive. It improves efficiency. It makes all the difference in timeline and budget. With Rig CallOut, companies can plan everything in real-time. No more surprises. No more back and forth phone calls. No more waiting. Game Changer.
Welcome to the 21st century oilfield. You’re going to like it here.